多层共挤流延膜生产中常见的问题
2024-12-25 11:14 来源:唯塑传播
在多层共挤流延膜的生产过程中,会遇到影响产品质量和技术性能的问题。这些问题不仅关系到生产的连续性和效率,还直接影响最终产品的质量。
模头设计不合理、熔体流动速率不一致或模具温度分布不均匀会导致薄膜横向厚度不均的问题。为解决此问题,需优化模具结构以确保熔体在模头内流动顺畅,并调整各段加热区的温度,使得整个模头的温度场更加均匀。
原料中含有的未完全塑化的高分子量树脂颗粒或外来杂质会导致薄膜出现过多的晶点。应严格控制原材料的质量,去除杂质,并适当提高机筒温度,保证所有成分都能充分融化。
卷绕张力设置不当或薄膜本身存在厚度差异可能导致边缘厚薄不均的现象。合理的做法是调整卷绕张力至适宜水平,并检查校正生产线上的测厚仪,确保薄膜厚度的一致性。
透明度差可能源于原料选择不当、加工条件不合适或工艺流程中有气泡残留。应选用高透明度的原料,根据材料特性调整最佳加工参数,并确保良好的排气,防止空气混入。
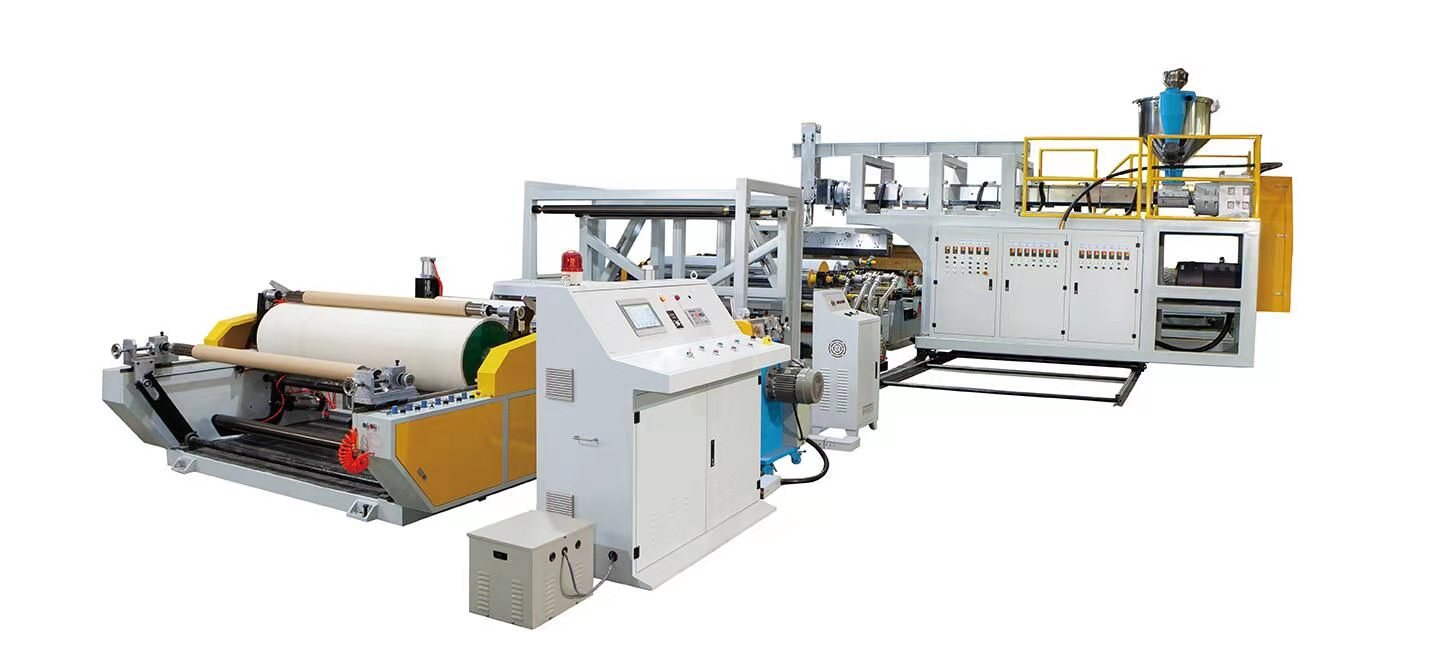
爽滑剂析出形成的致密层往往导致PE膜等薄膜表面出现过多白色斑点。建议选择耐高温、分子量高且质量好的爽滑母粒,以减少低温下的析出现象。
当爽滑剂添加量不够或其与材料体系不兼容时,可能会出现薄膜爽滑性不足的问题。需要增加适量的爽滑剂,同时选择与基材相容性良好的爽滑剂。
切刀位置不对或切割速度不稳定会造成薄膜卷端面不齐。定期校准切刀的位置,保持稳定的操作环境和切割速度是关键。
多层共挤过程中,不同层之间的材料兼容性不好、粘合力弱或存在相分离会导致界面不稳定。精确匹配各层材料的物理化学性质,使用适当的粘结层来增强层间结合强度,并维持稳定的生产工艺参数。
原料特性和加工过程中的温度过高、冷却速度过快等因素可能导致较大的收缩率。选择适合特定应用需求的原料,优化加工条件特别是控制好加热和冷却阶段的温度变化,以及适当降低牵引速度,给予材料足够的时间完成结晶过程。
生产企业需要不断积累经验,改进生产工艺,并且密切关注新材料和技术的发展趋势。
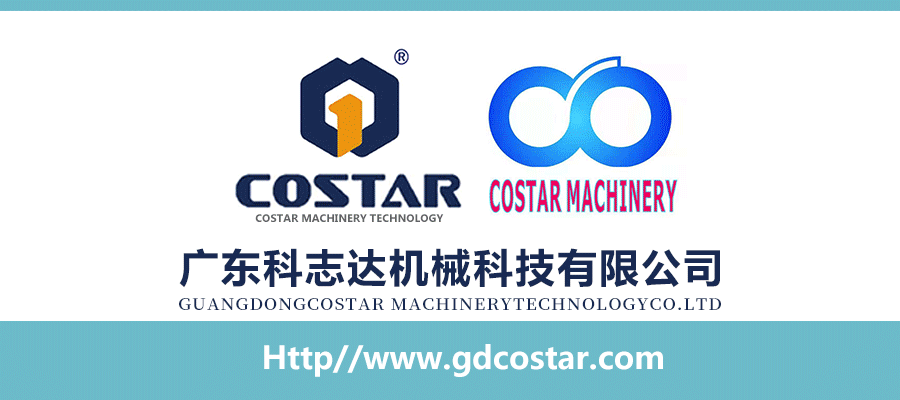